The importance of getting it right
More articles
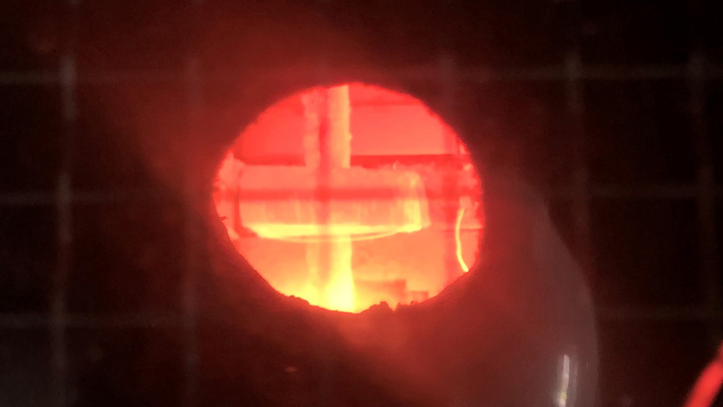
Passive fire protection and the importance of limiting temperature for steel structure
All materials become weaker when they get hot and structural steel is not an exception. Depending on the design of the structure, the steel will have a limiting or critical temperature.
What does this mean, and why is it important? How does it affect the amount of protection needed?
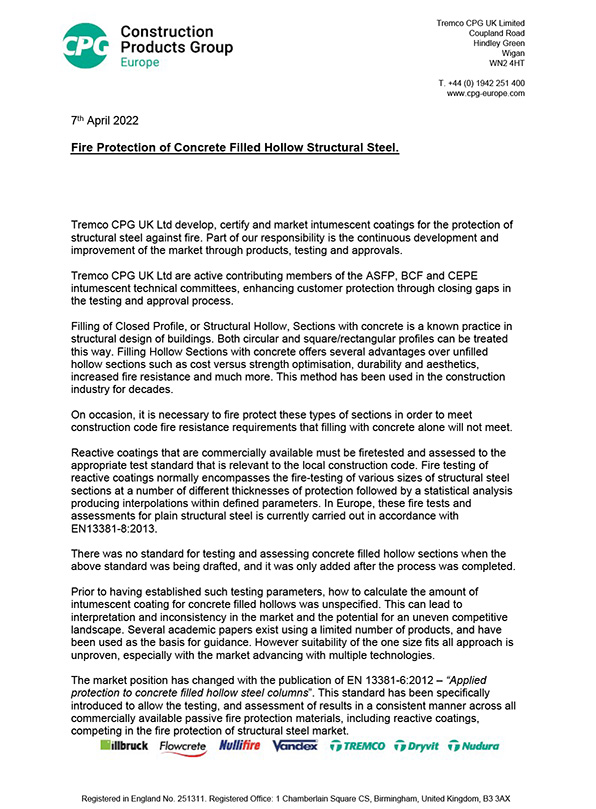
Fire protection of concrete-filled, hollow structural steel
Filling of closed profile or structural hollow sections with concrete is a well-known practice in the structural design of buildings.
It offers several advantages over unfilled hollow sections, such as cost versus strength optimisation, durability and aesthetics, increased fire resistance and much more, but it needs to be done correctly.
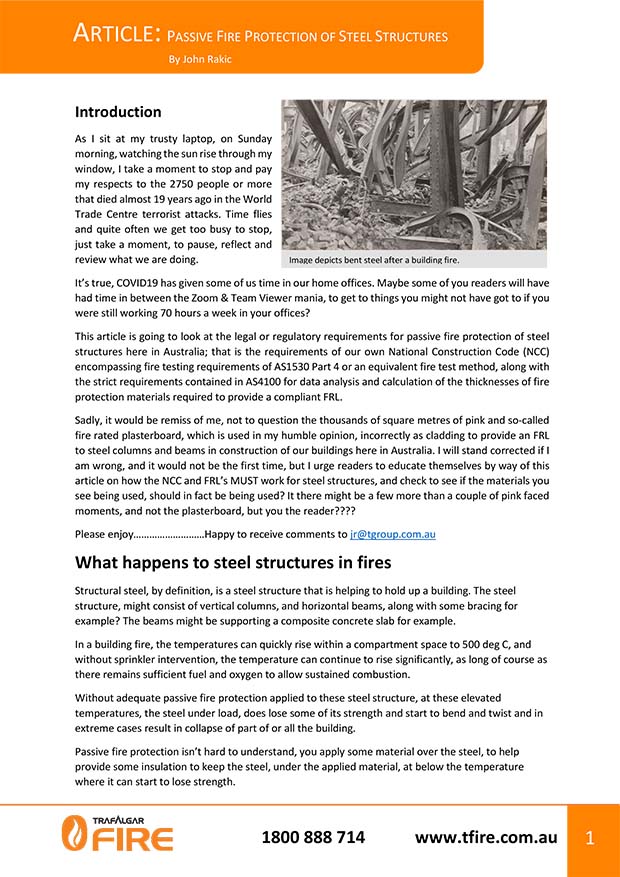
Passive fire protection of steel structures
A look at the legal or regulatory requirements for passive fire protection of steel structures in Australia, written by John Rakic, Managing Director of Trafalgar Fire.
John discusses the requirements of our own National Construction Code (NCC) encompassing fire testing requirements of AS1530 Part 4 or an equivalent fire test method, along with the strict requirements contained in AS4100 for data analysis and calculation of the thicknesses of fire protection materials required to provide a compliant FRL.
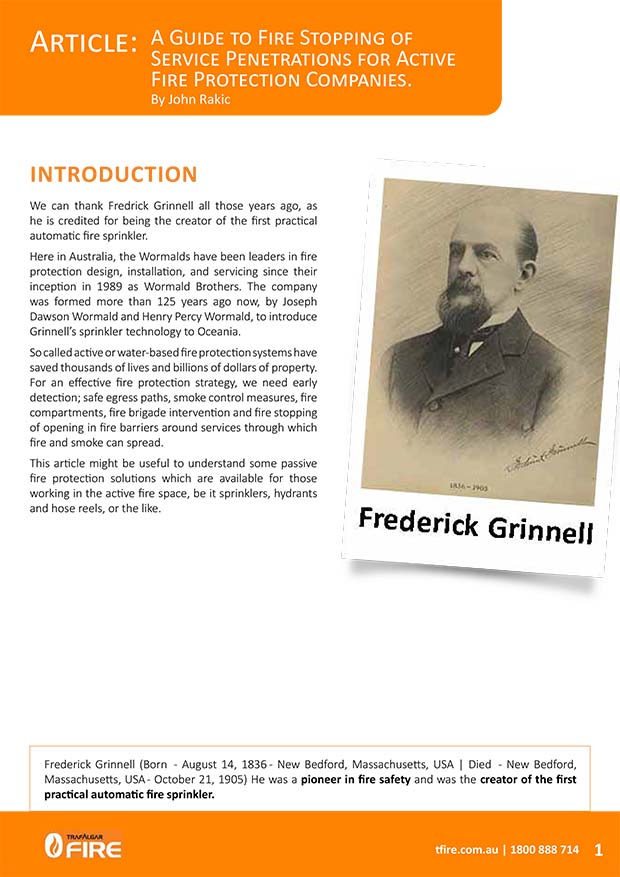
Fire stopping of service penetrations
There are many means through which heat can move from the fire side of a barrier to the non-fire side of a barrier. The fire barrier and/or the fire stopping material(s) themselves can (and do) get hot on the non-fire side in a fire, so choice and construction of fire barriers are important and differ depending on the fire rating duration.
This article assists in making those choices.
product datasheet library
We maintain a library of product datasheets as a ready-reference for you. This library is updated regularly but there are many products available so it isn't possible to provide every datasheet available. We do aim to provide the majority of datasheets for most the popular products.
still can't find what you're looking for?
If you can't find what you're looking for please let us know.
We aim for this website to be a comprehensive source of knowledge for intumescent coatings professionals or anyone with an interest in the subject.
We'll let you know via email when your request has been answered.